Understanding Welding WPS Requirements: Finest Practices and Techniques for Quality Welds
In the realm of welding, understanding Welding Procedure Specification (WPS) criteria is an important element that straight affects the quality and honesty of welds. Following these requirements ensures uniformity and reliability in welding end results. Nevertheless, achieving quality in welds goes beyond just comprehending the standards; it entails executing ideal methods and techniques that raise the craft to a level of accuracy and ability that distinguishes the standard from the outstanding. As we navigate with the intricacies of welding WPS requirements, uncovering key insights and approaches for achieving top-tier welds will be extremely important for welders seeking to excel in their craft and create welds that stand the test of time.
Comprehending Welding WPS Requirements
Recognizing WPS requirements is important for engineers, welders, and inspectors associated with welding procedures. By following WPS standards, welders can create welds that meet the required mechanical residential or commercial properties and structural integrity. Examiners depend on WPS documents to validate that welding treatments are being followed appropriately which the resulting welds are of premium quality. Engineers utilize WPS requirements to design welding procedures that ensure the longevity and dependability of welded frameworks.
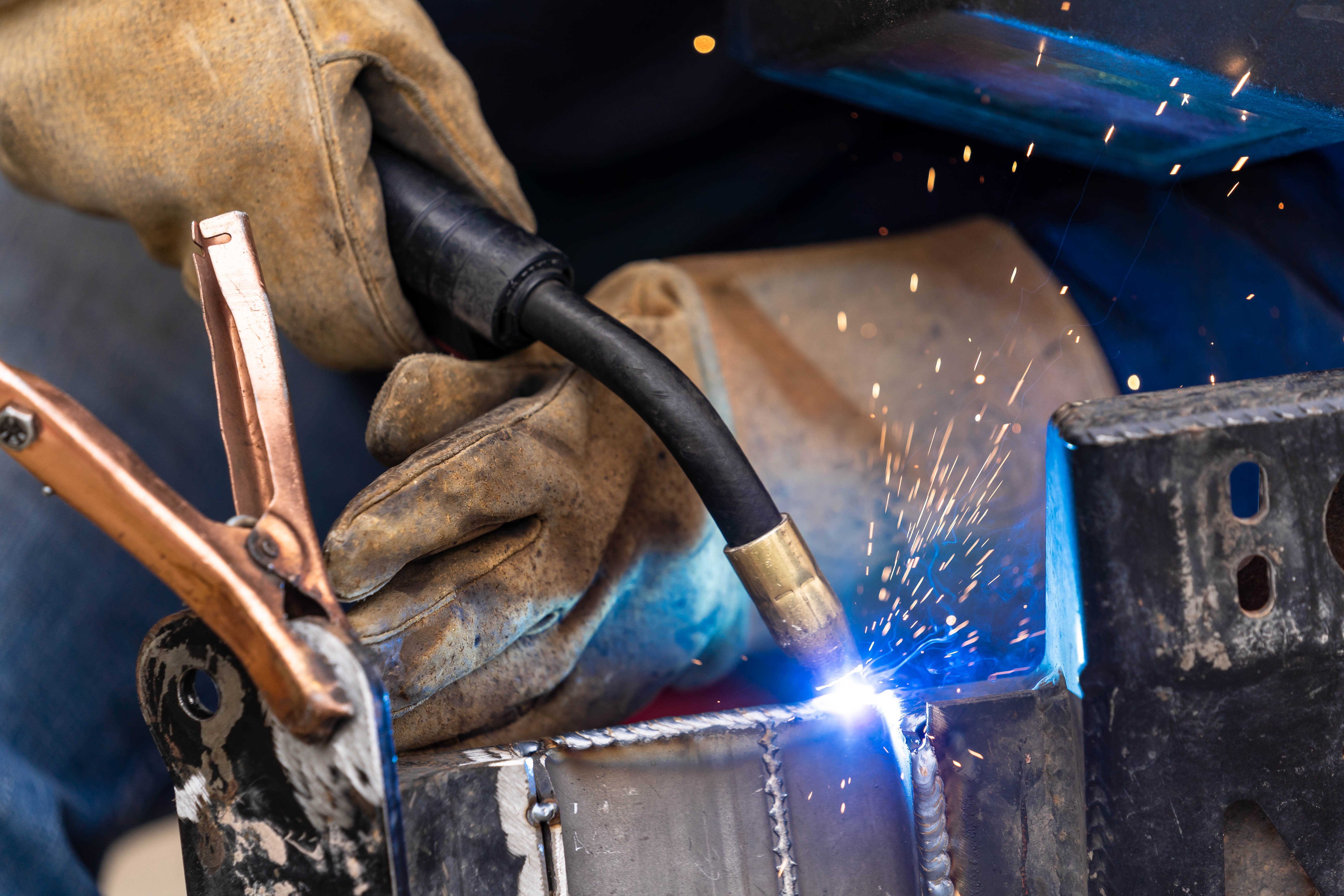

Essential Devices for Quality Welds
Understanding welding WPS standards is crucial for welders to successfully utilize the necessary tools needed for producing top quality welds. The kind of welding equipment needed depends on the welding procedure being used, such as MIG, TIG, or stick welding. Wire brushes and breaking hammers are important for cleansing the weld joint before and after welding to eliminate any pollutants that can affect the top quality of the weld.
Key Methods for Welding Success
To accomplish welding success, one need to understand the essential methods vital for creating top quality welds. Maintaining a stable hand and a secure welding position throughout the process is crucial to accomplishing accuracy and uniformity in the welds. By mastering these key techniques, welders can raise the quality of their job and accomplish welding success.
Ensuring Conformity With WPS Requirements
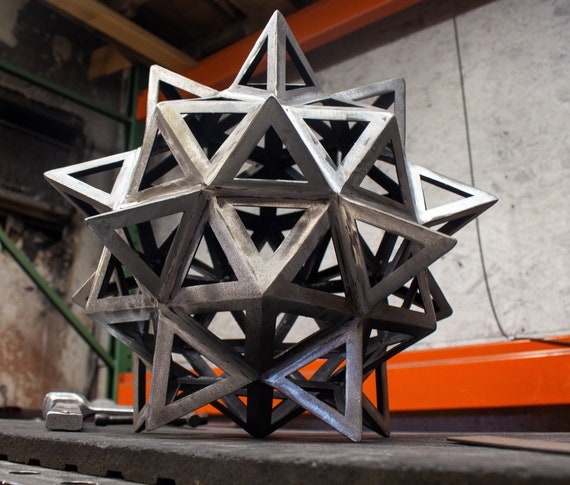
In addition, welders should go through training to familiarize themselves with the WPS requirements appropriate to their work. Regular audits and assessments should be performed to confirm that welding activities align with the recommended WPS standards. In addition, keeping thorough records of welding parameters, tools calibration, and inspection results is essential for showing compliance with WPS requirements - welding WPS. By carefully sticking to WPS criteria, welders can make certain that their job satisfies the needed go to my site top quality levels and contributes to the general success of the welding project.
Troubleshooting Common Welding Issues
When confronted with typical welding concerns, determining the origin reason is crucial for efficient troubleshooting. One prevalent issue is the presence of porosity in welds, usually triggered by contaminants such as corrosion, wetness, or oil. To resolve this, guaranteeing proper cleansing of the base steel before welding and making use of the correct protecting gas can considerably decrease porosity. Another issue often run into is lack of combination, where the weld fails to appropriately bond with the base material. This can stem from insufficient heat input or incorrect welding method. Readjusting specifications such as voltage, wire feed speed, or take a navigate to these guys trip speed can help boost combination. In addition, distortion, cracking, and spatter are usual check my reference welding obstacles that can be minimized via correct joint prep work, consistent heat control, and selecting the proper welding consumables. By thoroughly understanding these typical welding problems and their origin, welders can effectively fix problems and attain high-grade welds.
Verdict
In conclusion, grasping welding WPS criteria calls for a thorough understanding of the guidelines, making use of essential tools, and applying key techniques for effective welds. Making sure compliance with WPS requirements is crucial for producing quality welds and avoiding usual welding concerns. By adhering to ideal methods and practices, welders can achieve consistent and reliable lead to their welding jobs.
In the realm of welding, mastering Welding Procedure Spec (WPS) requirements is an essential part that directly influences the top quality and honesty of welds.When delving into the realm of welding practices, a crucial facet to comprehend is the significance and complexities of Welding Treatment Specification (WPS) requirements. WPS requirements provide a thorough standard for welding operations, making certain uniformity, top quality, and security in the welding process. The kind of welding device needed depends on the welding procedure being used, such as MIG, TIG, or stick welding.Attaining welding success with the mastery of crucial techniques necessitates a thorough understanding and adherence to Welding Treatment Specification (WPS) criteria.